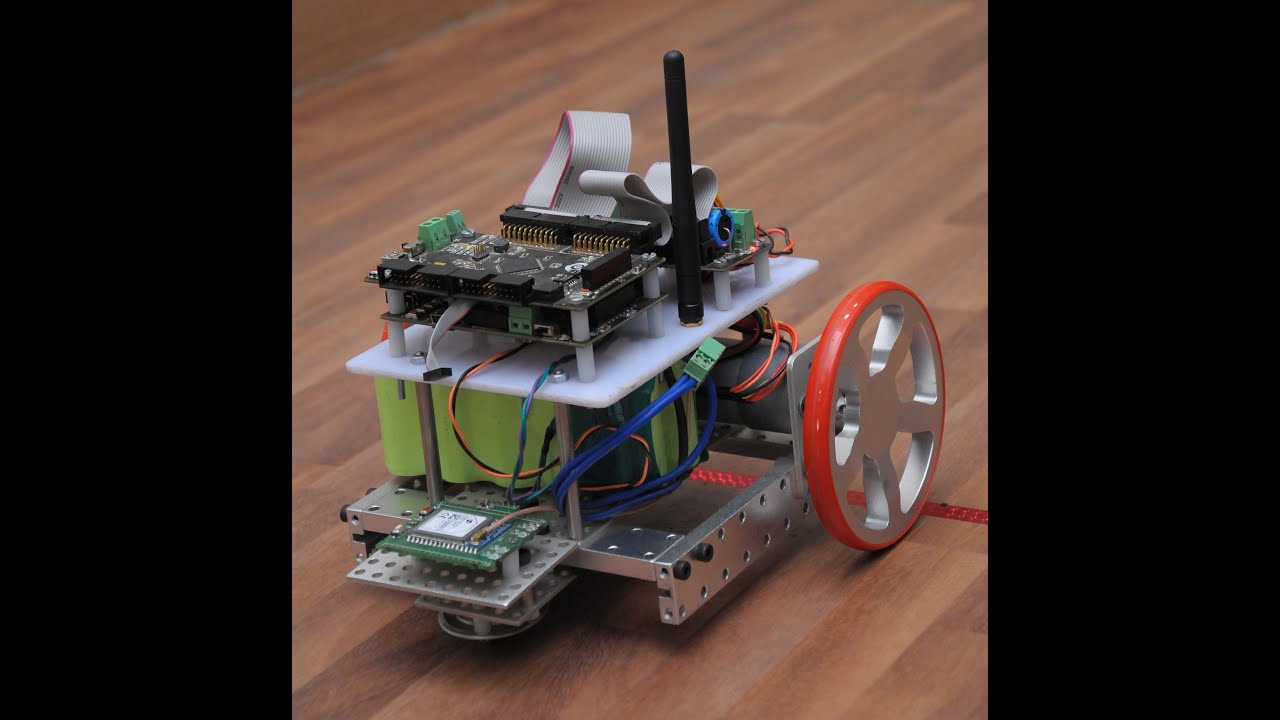
In order to design behaviors or
controllers for, for robots, we inevitably
need models of how the robots actually
behave. And we're going to start with one
of the most common models out there, which
is the model of a differential drive
mobile robot. So, differential drive
wheeled mobile robot has two wheels and
the wheels can turn at different rates and
by turning the, the wheels at different
rates, you can make the robot move around.
So, this is the robot we are going to
start with and the reason for it is
because it is extremely common. In fact,
the Khepera 3, which is the robot that we
are going to be using quiet a lot in this
course is a differential drive wheeled
mobile robot. But a lot of them out there
are, in fact, differential drive robots.
Typically, they have the two wheels and
then a caster wheel in the back. and the
way these robots work is you have the
right wheel velocity that you can control
and the left wheel with velocity that you
can't control. So, for instance, if
they're turning at the same rate, the
robot is moving straight ahead. If one
wheel is turning slower than another, then
you're going to be turning towards the
direction in which the slower wheel is.
So, this a way of actually being able to,
to make the robot more round. So, let's
start with this kind of robot and see what
does a robot model actually look like.
Well, here's my cartoon of the robot. The
circle is the robot and the black
rectangles are supposed to be the wheels.
The first thing we need to know is what
are the dimensions of the robot. And I
know I've said that a good controller
shouldn't have to know exactly what
particular parameters are because
typically dont know what the friction
coeficcient is. Well, in this case, you
are going to need to know two parameters.
And one parameter you need to know is the
wheel base, meaning how far away are the
wheels from each other? We're going to
call that L. So, L is the wheel base of
the robot. You're also going to need to
know the radius of the wheel, m eaning how
big are the wheels? We call that capital
R. Now, luckily for us, these are
parameters that are inherently easy to
measure. You take out the ruler and you
measure it on your robot. But these
parameters will actually play a little bit
of a role when we're trying to, to design
controllers for these robots. Now, that's
the cartoon of the robot. What is it about
the robot that we want to be able to
control? Well, we want to be able to
control how the robot is moving. But, at
the end of the day, the control signals
that we have at our disposal are v sub r,
which is the rate at which the right wheel
is turning. And v sub l, which is the rate
at which the left wheel is turning. And
these are the two inputs to our system.
So, these are the inputs, now, what are
the states? Well, here's the robot. Now,
I've drawn it as a triangle because I want
to stress the fact that the things that we
care about, typically, for a robot is,
where is it, x and y. It's the position.
And which direction is it heading in? So,
phi is going to be the heading or the
orientation of the robot. So, the things
that we care about are where is the robot,
and in which direction is it going? So,
the robot model needs to connect the
inputs, which is v sub l and v sub r, to
the states, somehow. So, we need some way
of doing this transition. Well, this is
not a course on kinematics. So, instead of
me spending 20 minutes deriving this,
voila, here it is. This is the
differential drive robot model. It tells
me how vr and vl translates into x dot,
which is, how does the x position of the
robot change? Or to y dot, which is how is
the y position, or phi dot, meaning how is
the robot turning? So, this is a model
that gives us what we need in terms of
mapping control inputs onto states. The
problem is, that it's very cumbersome and
unnatural to think in terms of rates of
various wheels. If I asked you, how should
I drive to get to the door, you probably
not going to tell me how what v sub l and
v sub r are, your probably g oing to tell
me don't drive too fast and turn in this
direction. Meaning, you're giving me
instructions that are not given in terms
of v sub l and v sub r, which is why this
model is not that commonly used when
you're designing controllers. However,
when you implement them, this is the model
you're going to have to use. So, instead
of using the differential drive model
directly, we're going to move to something
called the unicycle model. And the
unicycle model overcomes this issue of
dealing with unnatural or unintuitive
terms, like wheel velocities. Instead,
what it's doing is it's saying, you know
what, I care about position. I care about
heading, why don't I just control those
directly? In the sense that, let's talk
about the speed of the robot. How fast is
it moving? And how quickly is it turning,
meaning the angular velocity? So,
translational velocity, speed, and angular
velocity is how quickly is the robot
turnings. If I have that my inputs are
going to be v, which is speed, and omega,
which is angular velocity. So, these are
the two inputs. They're very natural in
the sense that we can actually feel what
they're doing which, we typically can't
when we have vr and vl. So, if we have
that, how do we map them on to the actual
robot. Well, the unicycle dynamics looks
as follows, x dot is v cosine phi. The
reason this is right is, if you put phi
equal to 0, then cosine phi is 1. In this
case, x dot is equal to v, which means
that your moving in a straight line, in
the x-direction, which makes sense.
Similarly for y, so y dot is v sine phi
and phi dot is omega because I'm
controlling the heading directly or the,
the, the, the rate at which the heading is
changing directly. So, this model is
highly useful, we're going to be using it
quite a lot which is why it deserves one
of the patented sweethearts. Okay, there
is a little bit of problem though because
this is the model we're going to design
our controllers for, the unicycle model.
Now, this model is not the differential
drive wheele d model, this is. So, we're
going to have to implement it on this
model and now, here we have v and omega.
These are our, the, the control inputs
we're going to design for. But here, v sub
r and v sub l are the actual control
parameters that we have. So, we somehow
need to map them together. Well, the trick
to doing that is to find out that this x
dot, that's the same as this x dot, right?
They're the same thing. This y dot is the
same as the other y dot. So, if we just
identify the two x dots together, then
divide it by cosine 5, we actually get
that the velocity v is simply r over 2, v
sub r plus v sub l or 2v over r is vr plus
vl. So, this is an equation that connects
v, which is the translational velocity or
the speed, to these real velocities. And
we do the same thing for omega. We get
this equation. So, only l over r is vr
minus vl. Now, these are just two linear
equations, we can actually solve these
explicitly for v sub r and v sub l and if
we do that, we get that v sub r is this
thing and v sub l is this other thing. But
the point now is, this is what I designed
for, this is what I designed for. So, v
and omega are design parameters. l and r
are my known measured parameters for the
robot, the base of the robot, meaning how
far the wheels are apart, and the radius
of the wheel. And with these parameters,
you can map your designed inputs, v and
omega, onto the actual inputs that are
indeed running on the robot. So, this is
step 1, meaning we have a model. Now, step
2 is, okay, how do we know anything about
the world around us?